Content ID
3 can-do farm shops
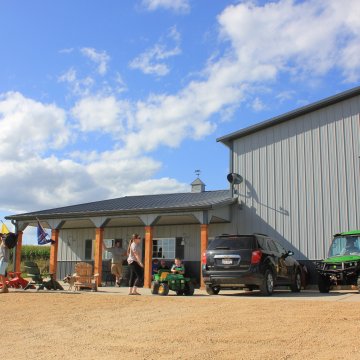
Take a look at these three Midwest farm shops after undergoing innovative structural changes that improve working conditions for their owners.
Raise-the-roof remodel
Madrid, Iowa
Nathan Todd is one of those people who makes a first-rate make-do engineer. The Madrid, Iowa, farmer wanted a shop and found the structure he needed in a post-and-beam storage shed his father erected in 1963. That 40×72-foot structure was in solid condition and its posts displayed no rot. The challenge to converting the shed to a shop was its 12-foot-high sidewalls.
The possibilities got Todd thinking. He wondered if there was a way to add 6 feet to the building’s sidewalls.
- READ MORE: Mike Korth: Designing the ideal farm shop
Determined to make it work, Todd innovated his own sidewall extension. His solution was to create those extensions using new 6×6s nestled in 3∕16-inch-thick C-channel irons that were 14 feet long. “I had the channel iron bent by a local metal fabricator so it would wrap around three sides of the existing post and post additions,” Todd explains. “Next I found a house mover to raise the structure. We made certain to pick a dead-calm day to elevate the building, that’s for sure.”
Once the mover had tied his jacks into the structure’s roof, Todd used a circular saw to cut the existing posts 4 feet above ground level. The structure was then elevated 6 feet. Todd moved the C-channels in place and filled the gap between the cut posts with new treated 6×6s. “We finished adding the extensions by that evening,” he recalls.
- READ MORE: The Baker shop houses multiple businesses
There was only one glitch in the extensions: The building’s old 6×6s were 515∕16 inches thick, but the new posts were 5½ inches thick. This left a nearly ½-inch gap between the new posts and the fabricated channel iron. “I cut ¼-inch furring strips from treated plywood to fill that gap,” Todd says. Once the new posts, channel irons, and furring strips were in place, Todd lagged them together with ½-inch bolts. “I had holes already drilled in the irons so all we had to do was bore holes in the posts and bolt it all together.”
Other improvements made to the existing structure included the addition of windows and overhead doors at the end and side of the building. “The existing end door was 18½ feet wide. I needed more clearance. So I reframed that end to accommodate a 24-foot-wide door. The 18½-foot side door was replaced with a new overhead door.”
As a final touch, Todd added a 9-foot-deep lean-to at the end of the shop to hold tools and supplies. The modified building was covered with new sheet metal and insulated with foam insulation.
- READ MORE: Shops with wash bays
The reframing and raising “cost the same as a new building shell, not including the concrete floor,” Todd explains. “The savings came in the fact that the old building had existing concrete that covered half the floor.”
Todd recalls he paid roughly $33,000 for new sheet metal, including a roof. The house mover charged him $9,000 to lift the building. “You could cut costs significantly if you left the existing tin on, adding new wainscoting metal at the bottom of the structure where you extended the building walls.”
You can contact Todd at ntoddfarm@gmail.com with any questions on his sidewall extensions.
Shop added to an existing machinery and livestock shed
Media, Illinois
Hugh Forbes and his son, Jeff, increasingly found themselves fixing equipment outside their then 24×50-foot shop. “As you might guess, our equipment had outgrown that building,” Hugh says, remembering nights suffering from an aching back after working underneath machinery on the cold ground.
So the Media, Illinois, farming team cast an eye across the farmstead at a 72×75-foot shed that served as machinery storage and a livestock building. The structure was solid, although it had dirt floors. More importantly, it had 16-foot sidewalls.
The Forbeses realized this was their future shop and set about remodeling it as such. “We never intended it to be a shop when we put up that building 40 years ago,” Hugh recalls.
Pouring a concrete floor and adding wall and ceiling insulation and sheet metal to interior walls were givens, but they wrestled with what to do about an entry door. “A hydraulic swinging door was the answer as it could be installed nearly at ceiling level, so it opens up at nearly 16 feet tall,” Jeff adds.
Originally the 72-foot-wide building consisted of the main structure with a 15-foot lean-to roof added on one side that served as a livestock loafing area. They enclosed the loafing area to provide space for workbenches, tools, and parts.
- READ MORE: 4 DIY farm shop implements
An industrial jib hoist, which was salvaged from a Mississippi River lock and dam site and was purchased by the Forbes duo for $600, was positioned in this area to create a machining spot.
Jeff had a service pit poured in the floor in front of the hoist. The pit is designed so vehicles can drive over the depression either lengthways or sideways. The sideways approach through a side service door is made possible thanks to heavy-duty bridges that span the width of the pit.
Mindful of the need for a good shop office that could also serve as a gathering area for family and friends, Hugh and Jeff added a 30×30-foot building that abuts the shop at one corner and is connected via a passageway from the shop to the office.
Office and meeting space addition
Orangeville, Illinois
Several years ago Kim and Mark Baker faced a dilemma. Expansion of their farming operation near Orangeville, Illinois, had run them out of office space.
They had created a small office in the loft of their 60×80-foot shop when it was constructed. Since then, however, their enterprise had grown. Already a thriving crop and dairy operation in addition to a Precision Planting equipment outlet that offers planter calibration services (bakerprecisionplanterworks.com), the couple’s sons, Chad and Zack, were involved in the farm and needed office space of their own as they sought to diversify the business even further. Three years ago the Bakers started growing hemp and have since established a hemp drying and distillation plant in nearby Monroe, Wisconsin.
- READ MORE: The best farm shop office
“The old office was barely big enough to take care of my needs,” Mark says, “and Kim was not crazy about us using the house for offices. So we looked to make an addition to the side of the shop to create an office complex.”
Working with the contractor that originally built the shop, the Bakers designed a plan for a 30×47-foot structure attached to the west side of the shop. The amount of space between the west side of the shop and the road limited them to a 30-foot-wide addition, Mark says.”
In the interior, the front of the office addition (which faces the parking area) is devoted to an open work area with computer stations around the room.
“We replaced the metal door that came with the building with a commercial glass door. It certainly wasn’t cheap. But it directs customers and visitors to come into the office,” Mark observes.
The rear of the office space is devoted to a meeting room complete with a kitchen. Corroded sheet metal siding “we found piled up and left to rust on a farm,” Mark says, serves as wainscoting and bright corrugated siding covers the ceiling. The door to the room is an old barn door that still operates on a sliding rail “both of which we found in an 1880s barn,” Kim points out, “and we used a hay track to create a chandelier for the meeting room. This makes a statement about our farming history for guests.”
- READ MORE: Farm shop heat options
The Bakers opted for in-floor heat (which they already had in their shop) for the office and meeting room. Air-conditioning is supplied through bright steel piping left exposed on the ceiling. “We liked that look when we saw it used in other offices,” Mark adds.
Tip of the Day
When you mow in a remote area